Issue No. 253〔Delivered Products & Systems〕
Construction of Municipal Solid Waste Treatment Plant
“Central Waste Management Center 70 t/d Incinerator”
Author
Teruyasu OKAMOTO*
Tomohisa OISHI*
Junichi SHIRATORI*
Kazuhisa KATAYAMA*
Yuki NITA*
Tomokazu TAKAHASHI*
- *
Ebara Environmental Plant Co., Ltd.
We delivered the municipal solid waste treatment plant Central Waste Management Center 70-ton/day Incinerator to the Oyama Wide-Area Hygiene Union, and completed its construction work at the end of September 2016. In the municipal solid waste treatment plant, our latest incineration system, the Ebara HPCC21 Grate-type Incinerator, operates at a low air ratio of 1.3 or below, generates up to 1 300 kW of electricity with boiler steam, feeds this electricity to existing facilities, and sells the excess electricity. Construction of this facility was a distinctive task, requiring work in a limited area while operating existing facilities.
Keywords: Municipal solid waste, Grate-type incinerator, Incineration plant, Environment, Low air ratio combustion, Renewable energy
1. Introduction
This construction work was the first-term work (construction, management, and operation of an incineration plant with a treatment capacity of 70 t/d) of the Basic Project for the Municipal Solid Waste Treatment Plant etc. for renewing an existing waste incineration plant (160 t/d). This project consisted of the aforementioned first term as well as a second term (addition, management, and operation of two incinerators with a treatment capacity of 70 t/d), and it was contracted in the form of a DBO package.
The facility was designed, procured, and constructed in a joint venture between Ebara Environmental Plant Co., Ltd., the representing company, and two construction companies (Sato Kogyo Co., Ltd., Itabashigumi Co., Ltd.) and was delivered to the Oyama Wide-Area Hygiene Union at the end of September 2016 (Figure 1).
The union treats waste from two cities and a town (Oyama City, Shimotsuke City, and Nogi Town) in Tochigi Prefecture, and the SPC (Special Purpose Company) in which Ebara invested has been managing and operating the facility for 20 years and six months since the facility started operation on October 1, 2016.

Fig. 1 Central Waste Management Center
70 t/d Incinerator
2. Overview of the Facility
2.1 Waste receiving system
The existing facilities of the Central Waste Management Center used a weighing scale (track scale) in two-way traffic. In addition, many vehicles carried municipal solid waste into the center, and during peak periods, the sites were surrounded by lines of vehicles waiting. Two weighing scales were added and integrated into the system with the existing weighing scale to reduce the time required for weighing when carrying in waste and carrying out ash and to relieve traffic of waste collection vehicles and vehicles carrying waste by citizen.
2.2 Solid Waste Treatment Plant
Figure 2 and Table 1 show a flow sheet of the Municipal Solid Waste Treatment Plant and an overview of the main systems, respectively.
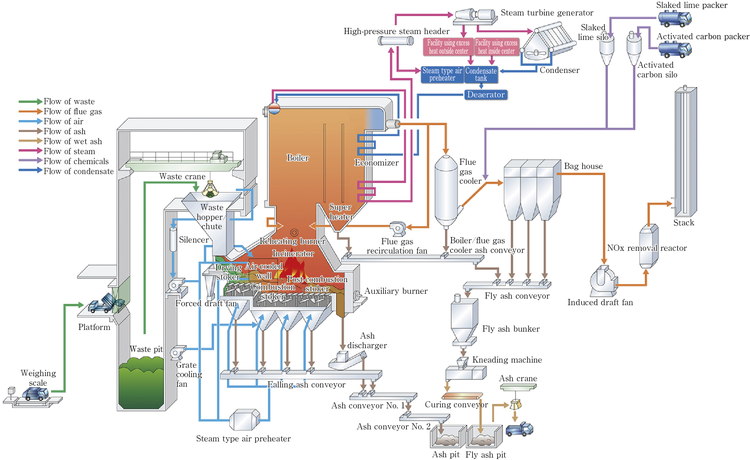
Fig. 2 Flow sheet of Municipal Solid Waste Treatment Plant
Receiving and feeding facility | |
Waste pit | Capacity: 2450 m3 (γ=0.143 t/m3 , for 5 days) |
Waste crane | Automatic crane×2 units |
Combustion facility | |
Incinerator | Continuous combustion type grate-type incinerator (Ebara model HPCC21) |
Treatment capacity: 70 t/d (1 incinerator) | |
Combustion gas cooling facility | |
Boiler | Natural circulation type water tube boiler with superheater |
Amount of evaporation: Up to 12.2 t/h×1 can | |
Steam condition: 3.0 MPa×320 ℃ (outlet of superheater) | |
Flue gas treatment facility | |
Flue gas cooler | Water injection type |
Dust collection system | Bag filter |
Denitration system | Selective non-catalytic reduction by ammonia water and denitration reaction tower |
HCl/SOx removing system | Dry type (slaked lime) |
Measure against dioxins and mercury | Dry type (Activated carbon) |
Waste heat utilization facility | |
Steam turbine | Extraction condensate type with 8-step impulse reducer |
Generator | 3-phase AC synchronous generator: 1300 kW |
Ash treatment facility | |
Burned ash | Carried out by pit and crane |
Fly ash | Humidified (chelated in case of emergency), carried out by pit and crane |
Effluent treatment facility | |
Industrial effluent | Not discharged in principle by reuse inside the center after coagulation sedimentation and sand filtration |
Domestic effluent | Discharged after treatment in combined private sewage private tank |
Waste foul water | Waste pit return system |
3. Construction Work Processes
Since the construction work was to be carried out with the existing facilities in operation, we constructed a temporary rampway to secure a new route for carrying waste into the existing facilities, and removed the existing rampway.The main milestones of the construction work are shown in Table 2, and the situation of the site during the construction work in Figure 3. The area marked with solid red lines is the construction site of this facility.
Contract | April 2013 |
Start of temporary construction work | November 2013 |
Start of use of weighing scale | April 2014 |
Start of facility construction work | April 2014 |
Start of plant construction work | May 2015 |
Start of receipt of electricity and commissioning | March 2016 |
Performance test | August 2016 |
Completion | End of September 2016 |

Fig. 3 Situation of site during construction work
4. Features of the Facility
4.1 Comparison with the existing incinerator
The existing waste incineration plant Central Waste Management Center 160 t/d Incinerator was constructed by Ebara-Infilco Co., Ltd. (note: merged with Ebara Corporation in 1994) and completed in March 1986. Table 3 shows the old and new specifications of the facility for comparison. The design value of the calorific value of waste of the new facility is significantly increased compared to the old facility. The old incinerator operated for more than 30 years after it was completed, and the design values of that time (quality of waste, etc.) were not in keeping with the current situation.
Item | Existing (160 t/d incinerator) | New (70 t/d incinerator) | |
Completion | March 1986 | September 2016 | |
Calorific value of waste (design value) [kJ/kg] Low quality: Standard quality: High quality: | 3 349 6 279 8 372 | 5 960 9 300 12 630 | |
Flue gas control value (design value) | |||
Dust | g/m3 (NTP)* | 0.05 or less | 0.01 or less |
Sulfur oxides | - | K value: 7 or less | 30 ppm* or less (K value = equivalent to 0.166) |
Nitrogen oxides | ppm* | 250 or less | 50 or less |
Hydrochloric acid | ppm* | 246 or less | 50 or less |
Carbon monoxide | ppm* | - | 1-hour average:100 or less 4-hour average:30 or less |
Dioxins | ng-TEQ/m3 (NTP)* | - | 0.05 or less |
Use of excess heat | |||
Heat supply outside center | GJ/h | - | 3 |
Power generation | kW | - | 1300 |
※All of the values shown above are based on dry gas; O2 = 12 % converted value.
4.2 Realization of high-efficiency energy recovery
To achieve satisfactory, stable combustion at a low air ratio and improve energy recovery efficiency, we adopted a flue gas recirculation system. In general, the bag filter outlet gas is used for flue gas recirculation in many cases, but this facility recirculates the economizer outlet flue gas by suction with a secondary fan. Thus, the flue gas treatment equipment was downsized and adapted to the site conditions, and the stirring and mixing of the gas inside the incinerator was accelerated and the generation of CO was prevented by increasing the amount of circulated gas by 20 to 30 % from the conventional level while maintaining the inside temperature of the incinerator, resulting in a reduction of the consumption of ammonia water used for denitration.The ratio of the flow rate of ammonia water with the design value assumed to be 1 is shown in Figure 4.

Fig. 4 Consumption of ammonia water when the amount
of flue gas recirculation increases
4.3 Adoption of renewable energy
The facility actively adopts renewable energy.
(1) Concentrator photovoltaic system (Figure 5 and Figure 6)
The facility was the first waste treatment facility to install a concentrator photovoltaic system, which collects sunlight with a special condenser lens and generates electricity while tracking the movement of the sun, instead of ordinary solar panels.
The concentrator photovoltaic system can generate electricity with high efficiency in sunshine, but unlike ordinary solar panels, it does not output any electricity at all (0 kW) in cloudy weather.
The system, in general, is used in regions with a large quantity of direct solar radiation, such as desert areas close to the equator, but was installed with the aim of raising the awareness of elementary school students who visit the facility on field trips.

Fig. 5 Photovoltaic system
(in the morning)

Fig. 6 Photovoltaic system
(in the afternoon)
(2) Lighting ducts (Figure 7 and Figure 8)
The lighting ducts guide light into the room without converting sunlight into electricity. Unlike top lights, these lighting ducts look like ordinary lighting equipment in appearance and do not impair the indoor atmosphere. They can also secure some light even in cloudy or rainy weather. They are installed in the passage for visitors.

Fig. 7 Lighting ducts (daylighting units)

Fig. 8 Lighting ducts (indoor illumination)
5. Status of Operation of the Facility
The Municipal Solid Waste Treatment Plant started receiving waste on June 1, 2016, and actual load incineration commissioning on June 10. It completed a pre-use self-inspection as a power generation plant by the end of July 2016 and performed a preliminary performance test in July 2016 and a delivery performance test in August 2016.
Table 4 shows the measurement results of flue gas and other data obtained in the delivery performance test.
The oxygen concentration at the outlet of the boiler was 3.4 % on average (wet basis), and the facility achieved stable operation at an air ratio of 1.3 or less. Carbon monoxide and nitrogen oxides were 11 ppm and 36 ppm, respectively, on average, which were far below the judgment criteria. Note that all of the judgment criteria were met satisfactorily under other pollution control conditions concerning dioxins, etc.
Item | Criteria | Results | Judgment | |
Day 1 | Day 2 | |||
Incineration capacity | 70 t/d or over (100 % or over) | 100% or over | 100% or over | Passed |
Dust concentration | 0.01 g/m3 (NTP) or less | Less than 0.001 | Less than 0.001 | Passed |
Sulfur oxides | 30 ppm or less | 7 | 11 | Passed |
Nitrogen oxides | 50 ppm or less | 37 | 35 | Passed |
Hydrochloric acid | 50 ppm or less | 30 | 31 | Passed |
Carbon monoxide (4 hours) | 30 ppm or less | 10 | 11 | Passed |
Dioxins | 0.05 ng-TEQ/m3 (NTP) or less | 0.00041 | 0.00019 | Passed |
6. Supply of Electricity by New Power Generation Facility
The electricity generated by this facility covers the power required on the premises and is supplied to existing facilities. During the daytime on weekdays, when the existing facilities are in full operation and the recycling plant, in particular, is operating, this facility needs to purchase electricity, but it sells excess electricity when only the 70 t/d incinerator is operating.
This facility sells electricity to our new power producer and supplier (PPS), Oyama E-Service Co., Ltd., to realize local generation and local consumption of electricity (Figure 9).

Fig. 9 Supply of electricity by power producer and supplier
7. Conclusion
This facility was completed on September 30, 2016 and is operating in good condition. We are determined to ensure that the facilities are managed and operated smoothly for a long period of the next 20 years and six months, and long into the future, and to contribute to the establishment of a sustainable society.
In conclusion, we would like to express our sincere gratitude to the staff members of the Oyama Wide-Area Hygiene Union and to all those who offered a great deal of advice and cooperation to us in the construction of this facility.
References
1) Waste Incineration Plant – Delivered to the Oyama Wide-Area Hygiene Union, Ebara-Infilco Engineering Review No. 94, pp. 63-64 (March 1986).
2) Teruaki TSUKAMOTO, Masamitsu SASE and Minoru SASAKI, “Operation of the HPCC21 Stoker System at Kawasaki City Ozenji Municipal Solid Waste Treatment Center”, Ebara Engineering Review No. 236, pp. 30-36 (July 2012).
3) Naoto AKIBA and Tetsuji IGUCHI, “Stoker-Type Waste Incineration Plant for Iwamizawa, Hokkaido Construction and Delivery of Iwamizawa Environment Clean Plaza”, Ebara Engineering Review No. 249, pp. 14-20 (October 2015).
4) Keisuke TSUKAMOTO, Kenichi NISHIYAMA, et al. Construction of Municipal Waste Treatment Plant “Clean Plaza Yokote”, Ebara Engineering Review No. 252, pp. 69-74 (October 2016).
Recommended articles
Inquiry about Ebara Engineering Review